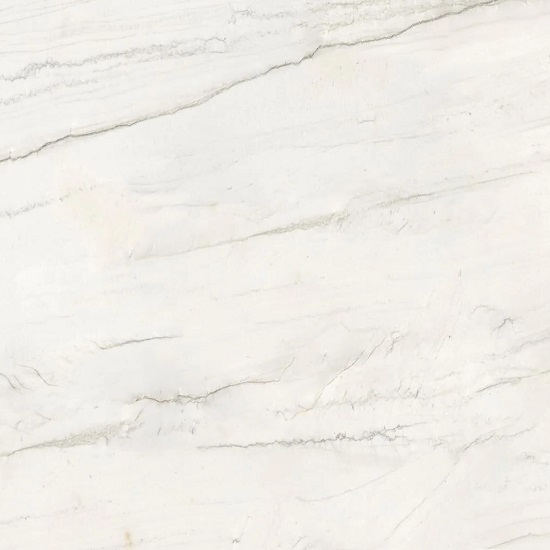
In stock
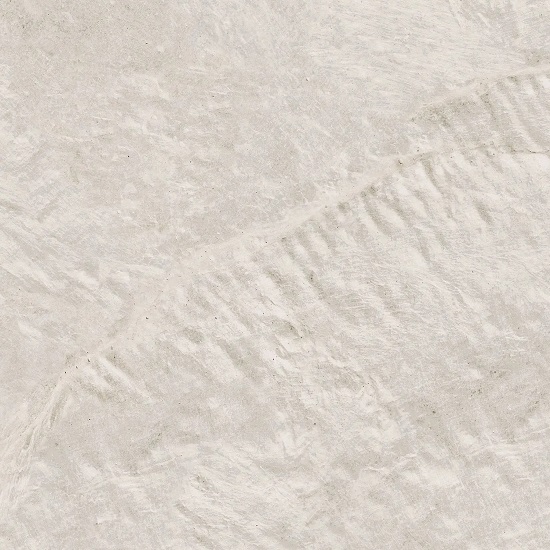
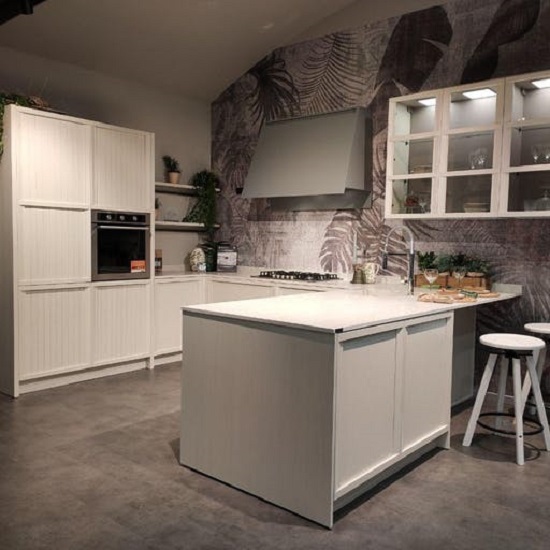
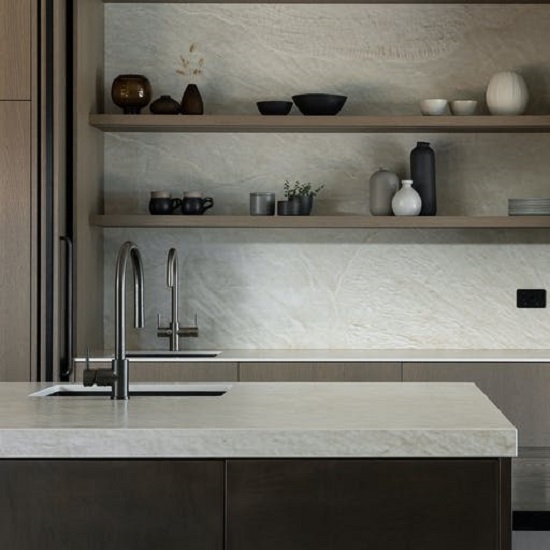
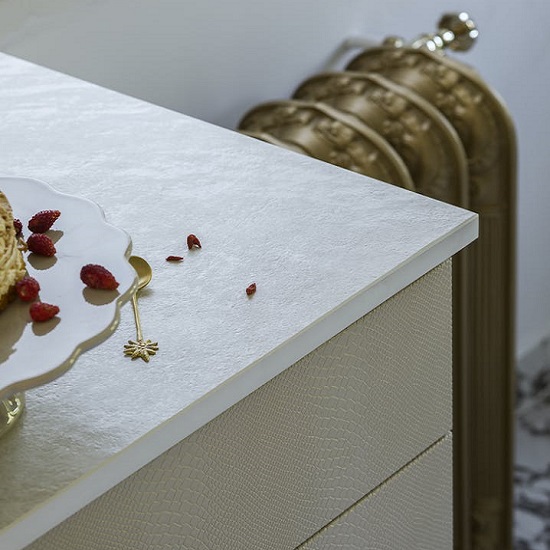
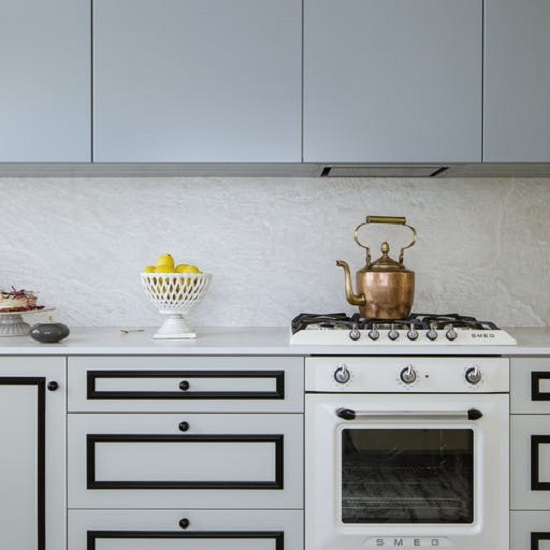
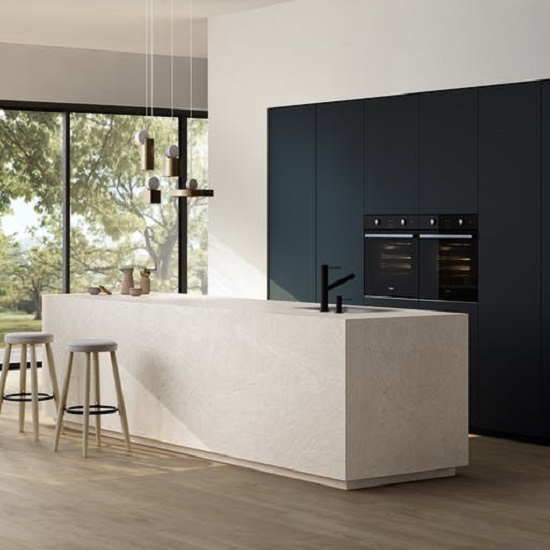
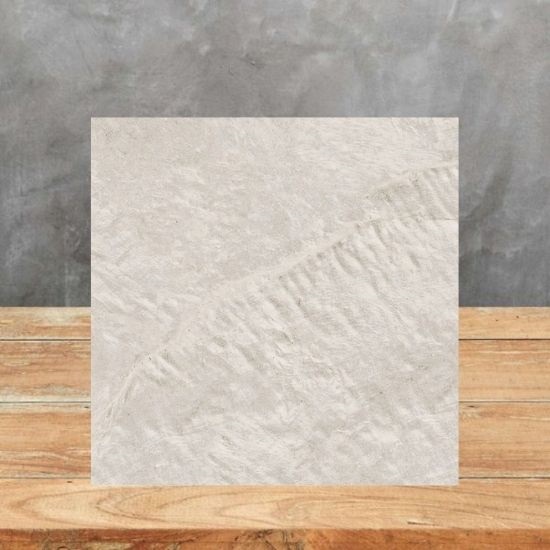
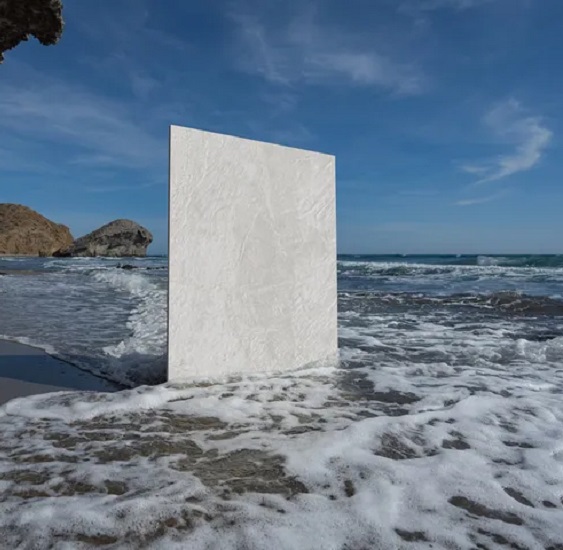
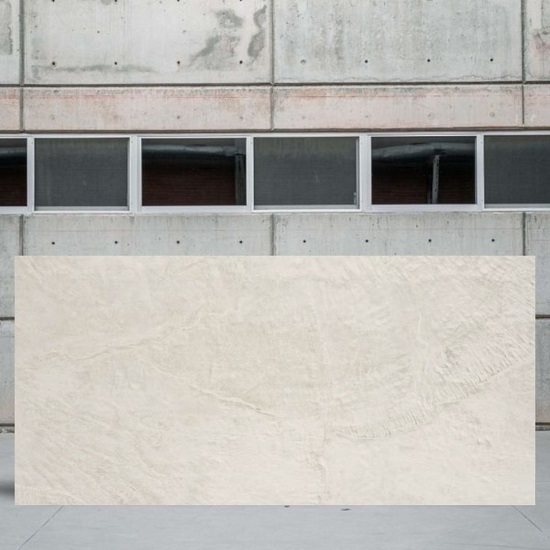
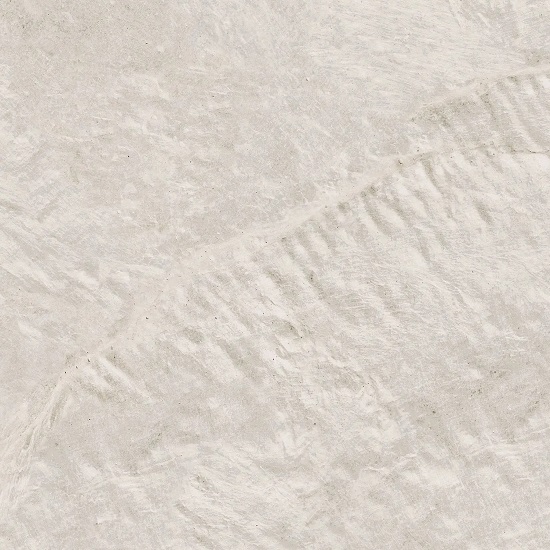
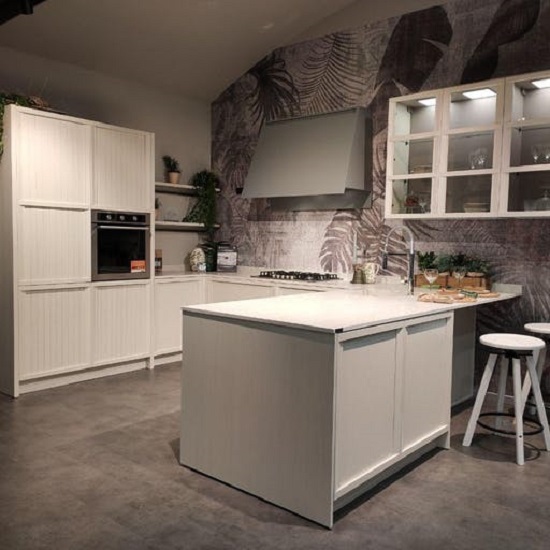
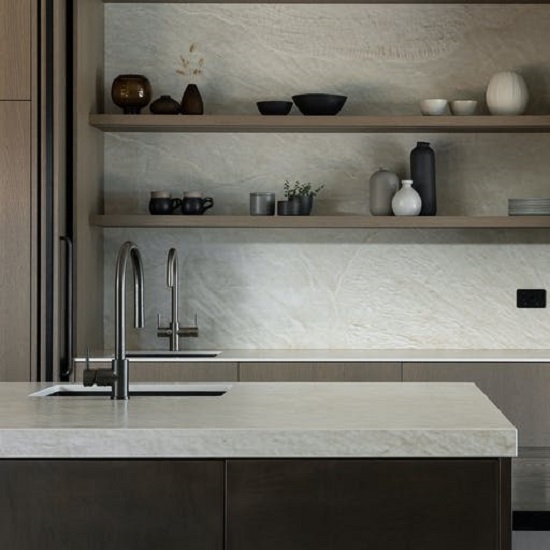
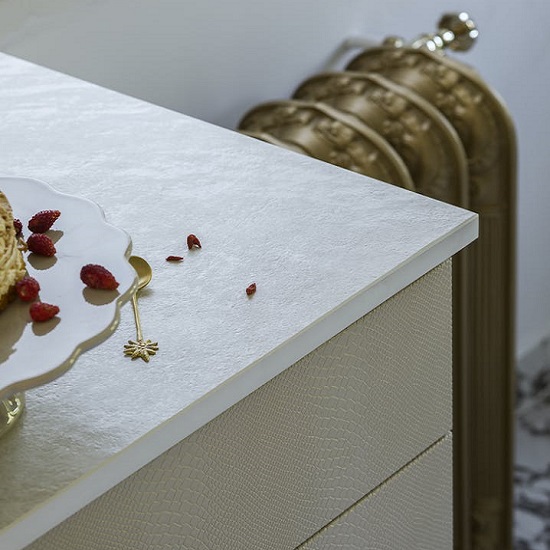
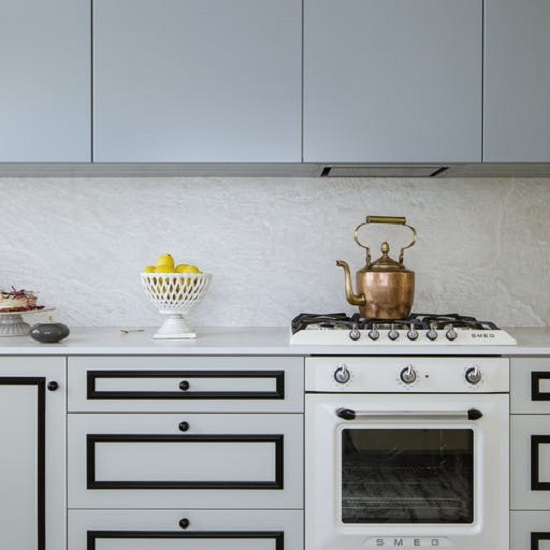
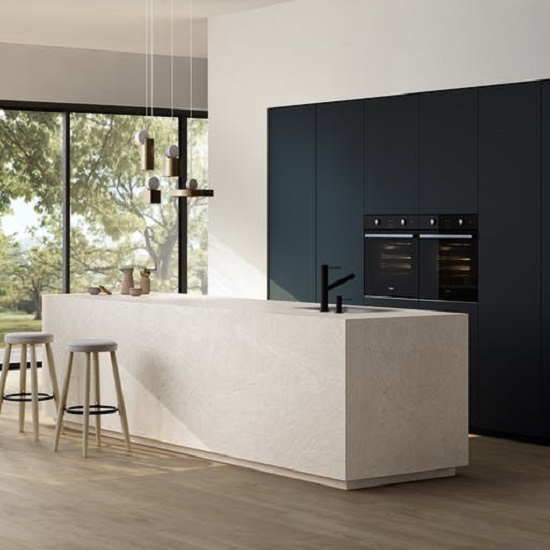
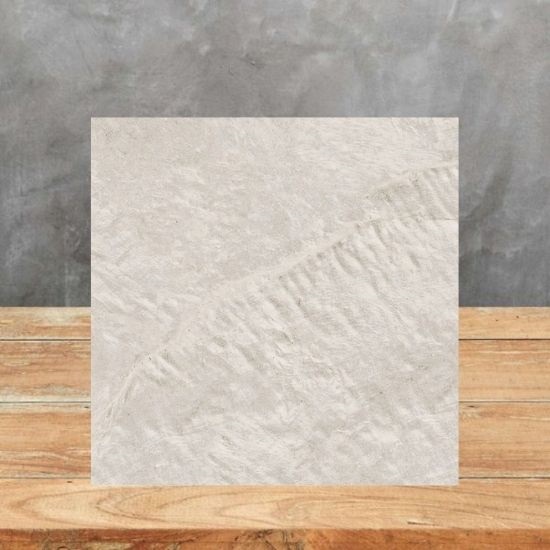
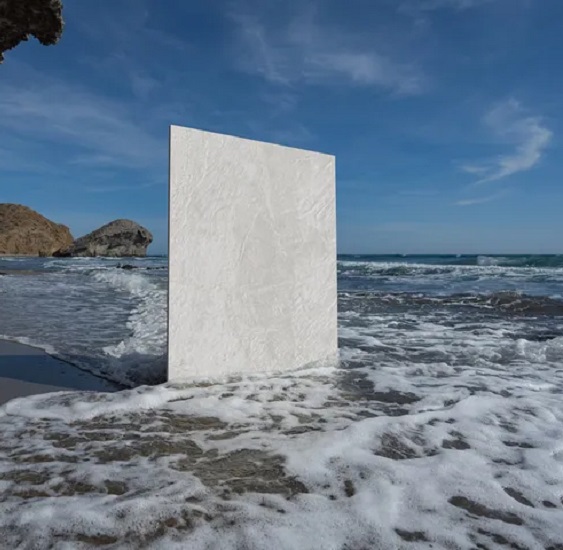
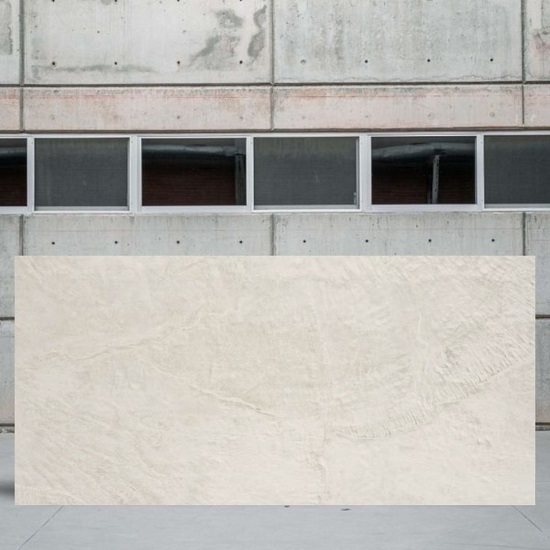
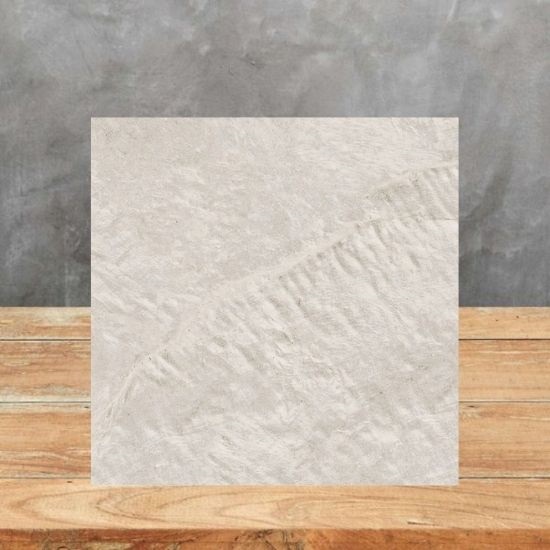
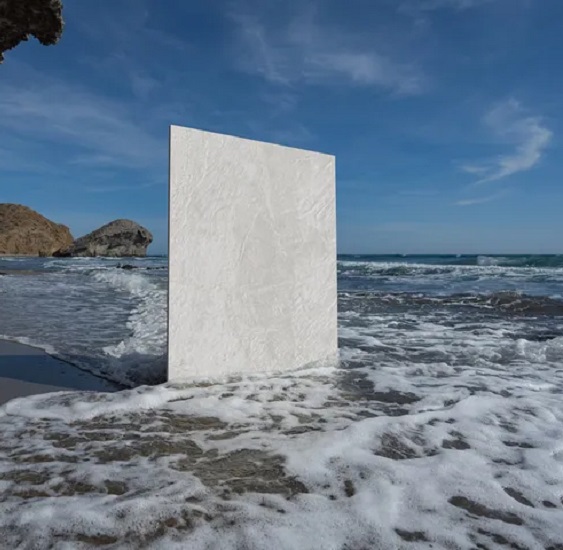
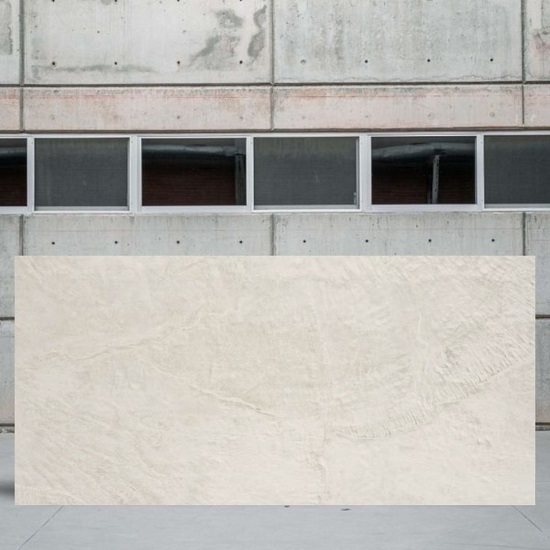
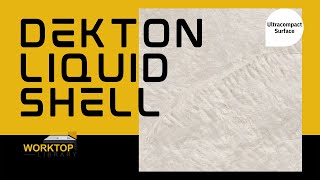
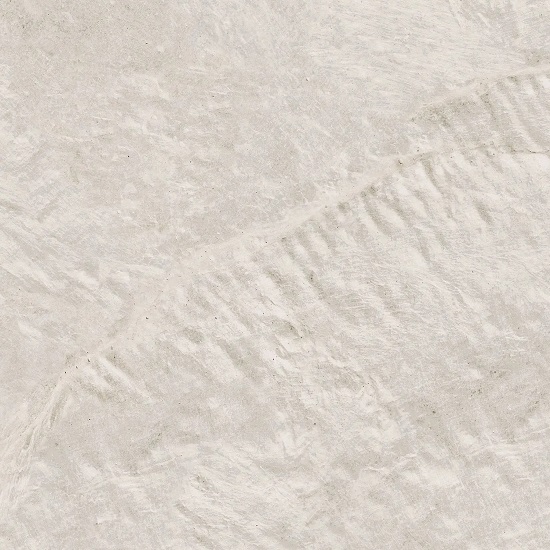
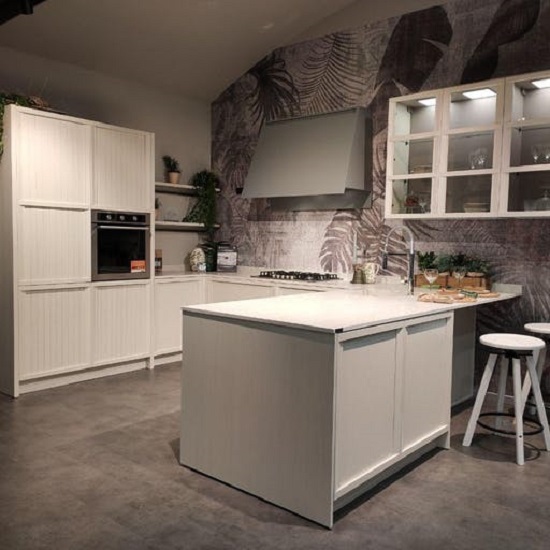
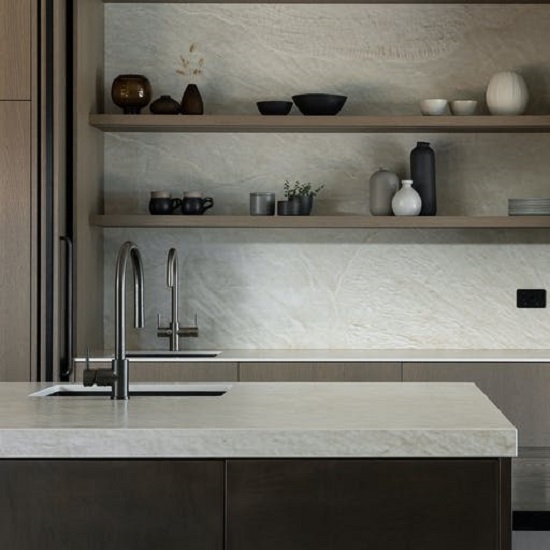
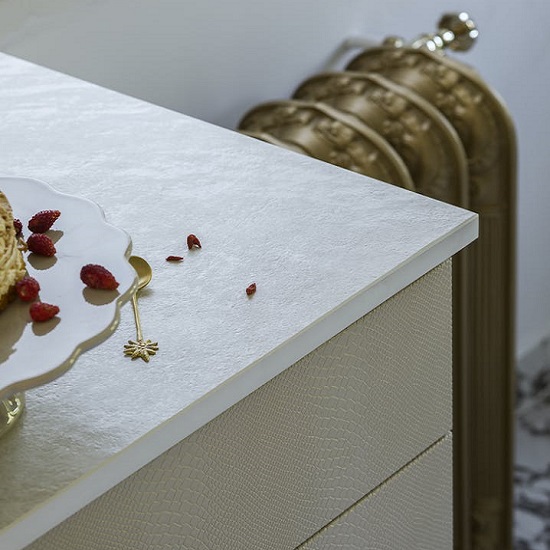
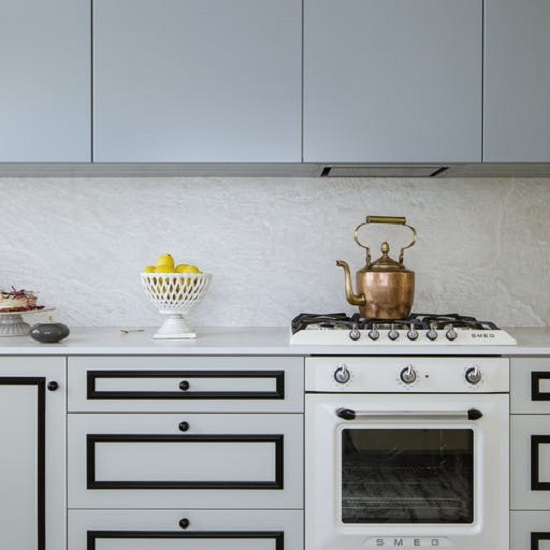
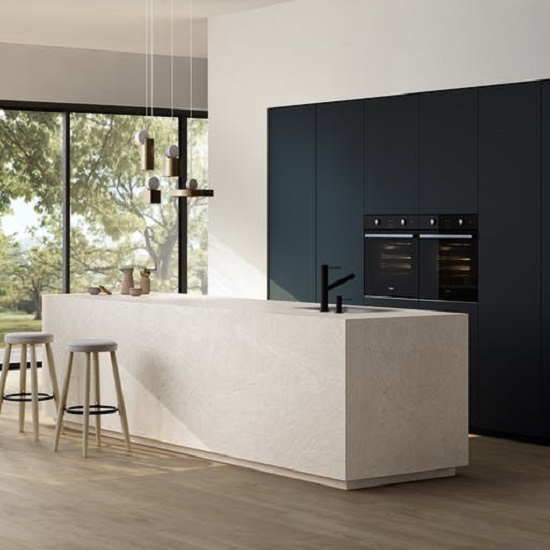
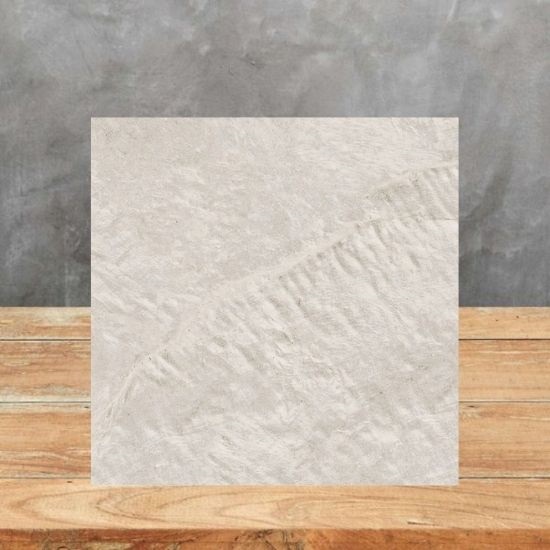
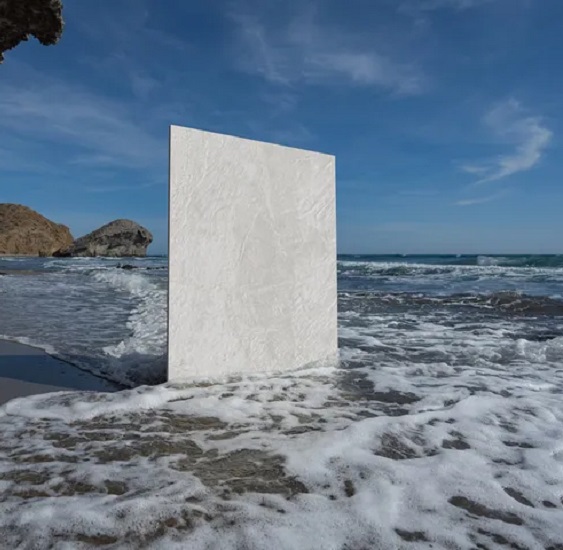
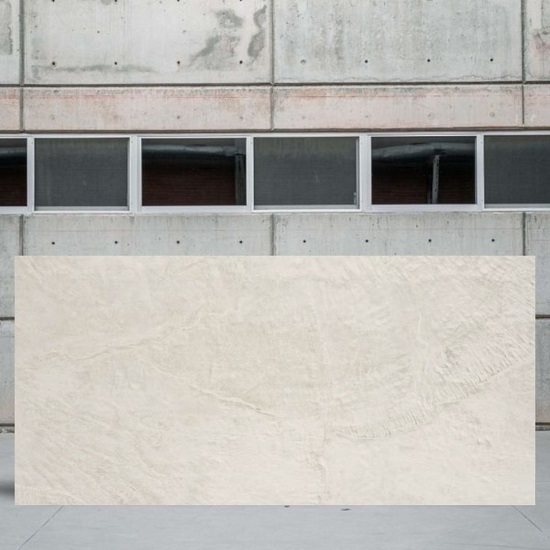
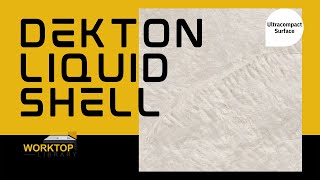
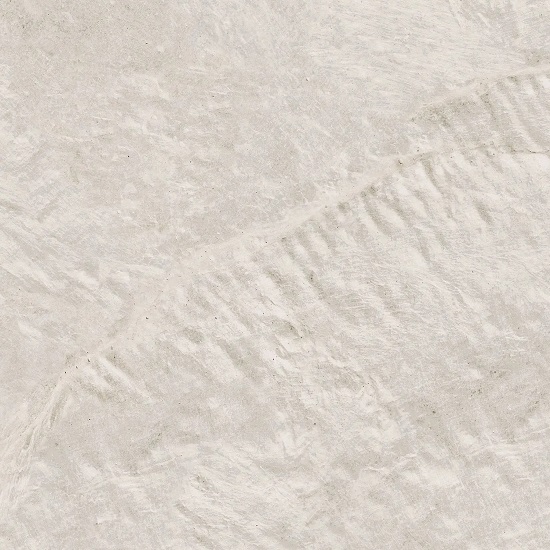
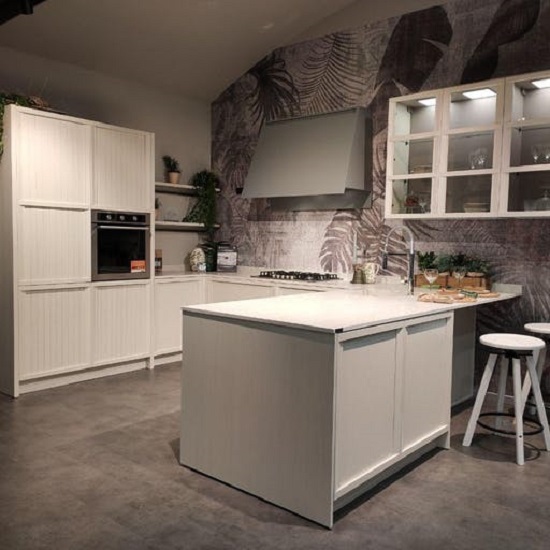
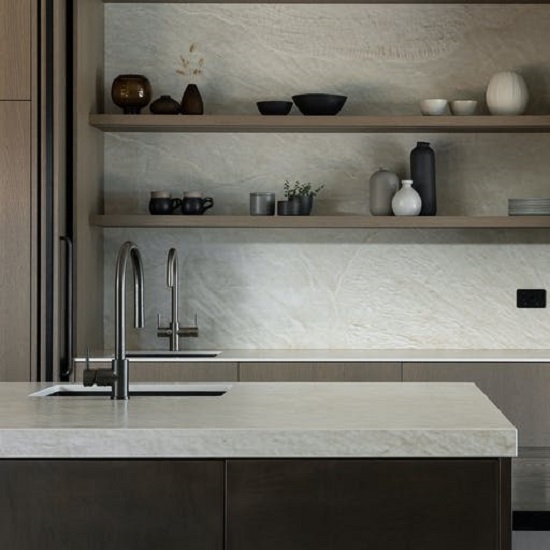
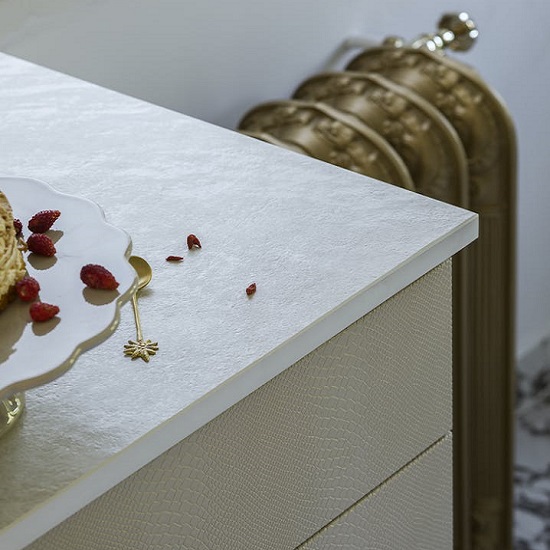
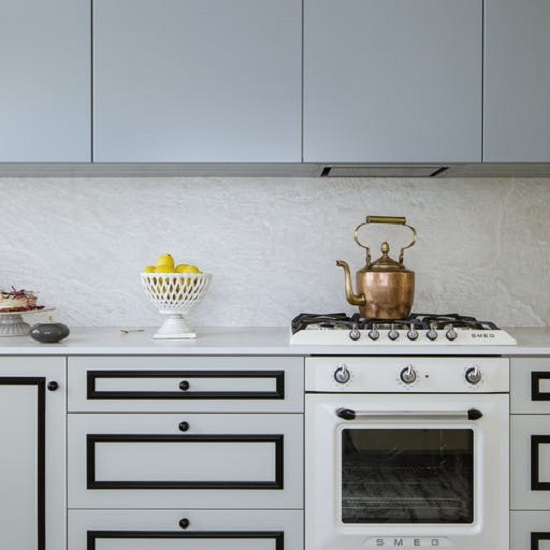
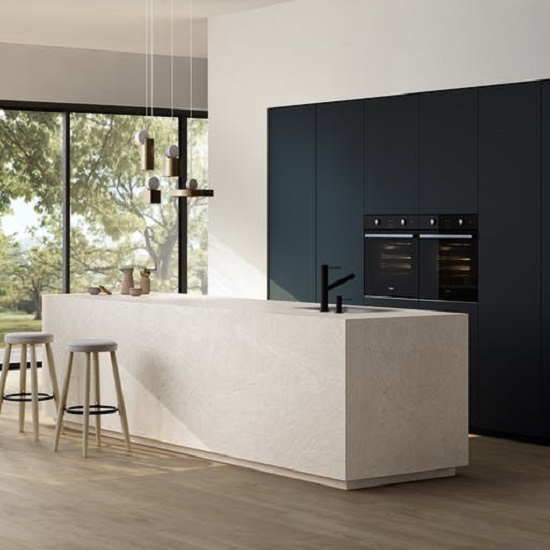
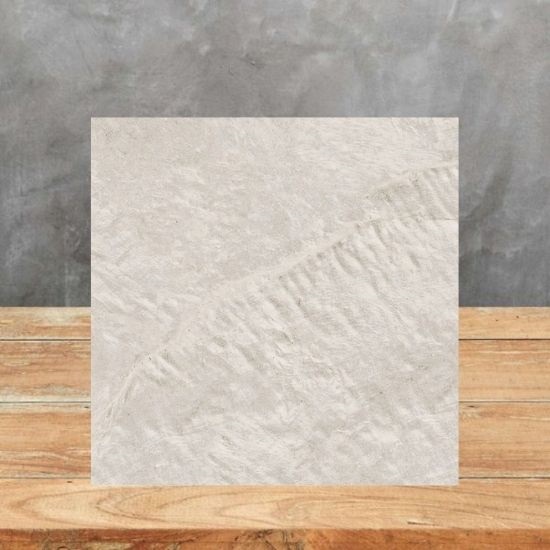
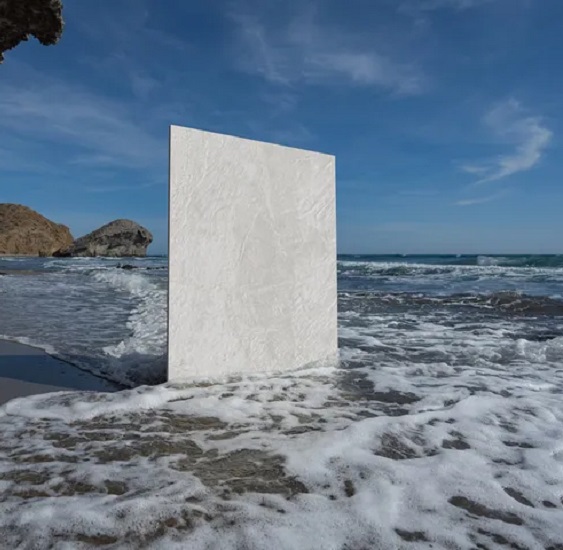
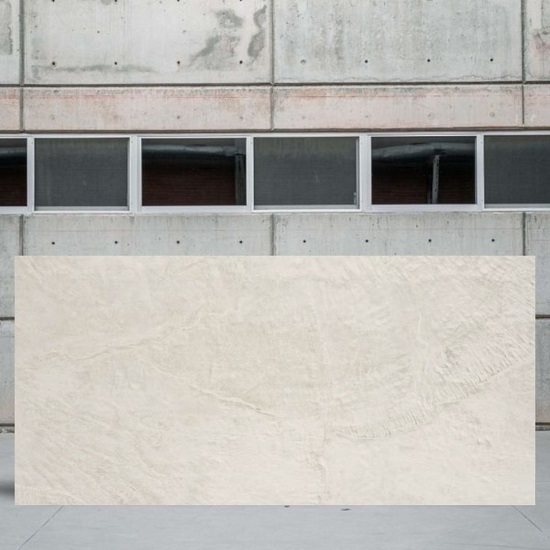
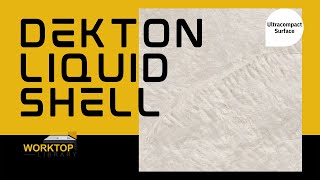
Dekton Liquid Shell
Our Dekton Liquid Shell worktop highlights the fossils and minerals that live under the ocean waves by embracing refinement and tenderness. Read More
Dekton Liquid Shell highlights the fossils and minerals that liveunder the ocean waves by embracing refinement and tenderness. The sea resembles the cyclical nature of the world, with its steadyflow that soothes and creates new patterns and flat surfaces with each moving wave. In conjunction with the rhythms of the water, the moonlight inspiresthe creation of Liquid Shell. The iridescent colour is a changing white tonewith an undulating design of the seafloor.
With revolutionary design and manufacturing blended with gorgeous raw materials, the 322 x 144 cm slabs offer a new way to decorate interiors and outdoors without compromising perfect functionality. You can choose this sintered stone design in thicknesses of 8 mm, 12 mm, and 20 mm, and a gorgeous texture known as ‘Velvet finishing’. If you prefer a rustic look, you can also select the ‘Textured Matte’ finish for additional visual impact.
Dekton Liquid Shell Description: Ancient Fossils like you’ve never seen
Dekton Liquid creates continuous, moving, extending, and contemporary surfaces, perfect for floating shelves, expansive kitchen islands, and bathroom vanities.
Liquid Shell offers an opaque white backdrop with stunning cream undertones. In addition, it elegantly displays interfacial shine corresponding to its textures’ hues, giving it a beautiful and refined shade. Its muted white integration evokes memories of a shimmering, swirling shell-like material, finely buffed to produce an innovative and modern velvet finish worktop.
Liquid Shell Worktops: high on performance, low on weight
Dekton Liquid Shell comprises raw materials that are crushed, pressed and heated to result in a sintered stone. Sintering is a sped-up variant of natural stones’ changes over millennia, industrially reduced by only forty-eight hours. Cosentino uses heat and pressure to compress and produce the solid ultracompact worktop material with several benefits.
A Dekton Liquid Shell countertop provides additional advantages over other worktop materials such as quartz, marble, and granite. In addition, the slabs undergo treatment during the production process to offer advanced stain-resistant nanotechnology, UV ray protection, water resistance, impact resistance, and heat resistance.
Our Liquid Shell ultracompact surface has outstanding finishing, long-lasting endurance, and stunning looks. Indeed, this kitchen worktop’s feel and visual experience evoke the beauty of organic materials.
Sustainable Worktops with Lots to Love and Less to Worry About
Liquid Shell is part of this collection of work surfaces that boasts the International EPD System (International Environmental Product Declaration), which evaluates greenhouse gas emissions, the efficiency in raw materials and energy consumption, and the reduction in waste generated. In addition, Dekton products achieved the status of being Carbon Neutral materials goal of the SDGs of Agenda 2030 for Sustainable Development.
Dekton Liquid ShellSizes, Thicknesses, Finishes
- Slab Size: Dekton’s huge slab size of 3,200 x 1,440 mm covers many areas, minimising the number of joints. In addition, it makes the entire design and installation procedure more efficient and less expensive in terms of installation material usage and effort during its installation. Finally, it includes maintenance, replacement, and restoration. For example, Worktop suppliers must be more careful with grouts and edges when dealing with small panels. Also, having smaller stone pieces means more cuts, more sides to polish, and, ultimately, more upkeep. With Liquid Shell, you will forget about all of these nuances.
- No Joints: Similarly, full-size Dekton slabs require cutting, cleaning, maintenance work, and steps to increase physical attractiveness. Designers have the opportunity to incorporate natural beauty into these essential pieces in a consistent way by eliminating joints and seams. The large stone slabs have beautiful veins, fissures, and patterns best appreciated on a single part of the Dekton slab cut from a single sheet.
- Thicknesses: The stone countertop brand lets you choose from the highest number of thickness options. You can select Dekton from thicknesses of 0.4 cm, 0.8 cm, 1. 2 cm, 2 cm, and 3 cm.
- Finish: Dekton Liquid Shell belongs to the Liquid Collection and is available in Velvet Finishing and Textured Matte, two natural finishes that suit any design style.
Caring for the nicest, lightest, strongest Dekton Worktop ever
Dekton is a 100% chemical and stain-resistant surface making it the perfect kitchen worktop. A great companion for any activity.
Daily cleaning: For daily cleaning, use a glass-cleaning spray. Then, dry with a paper towel or cloth.
Getting Rid of Tough Stains
- The matte finish is unaffected by any household substance or chemical, making it extremely difficult to stain.
- The polished finish may stain only when in contact for over 24 hours with a strongly coloured, abrasive, or sticky chemical. In these situations, you can use cream detergents with abrasive particles (i.e. CIF Cream) or solvents (i.e. acetone or universal solvent)
Dekton Manufacturing: State of the Art Technology
The Dekton Liquid Shell making process entails 7 (seven) key stages during its production:
- Raw materialpreparation: the company examines the raw materials for quality and usability. To avoid cross-contamination, the manufacturer keeps all the natural ingredients separately. Then, it moves these materials onto hoppers and purification machines with a conveyor belt.
- Mills and hybridisation: The manufacturer transfers the DEKTON formula from the hoppers or purification systems to a moist grinding process. It blends the different raw ingredients precisely and ground to specific particle sizes. The particle size entirely controls the pace and direction of the chemical process that produces DEKTON. It also influences the product’s ultimate qualities. Following a specific stabilisation time, this combination is kept separately before application.
- Pigmentation: The company uses a sophisticated mixer, diluters, and stirrers during the pigmentation process. Dependent on the colour or finish, this technology can blend inorganic colours with the remainder of the DEKTON composition. Because these pigments are also a component of the material’s chemical process, chemical quality control is comprehensive and demanding.
- Atomisation: The manufacturer atomises and dries the previously coloured formula until it achieves a particular size, grain shape, and humidity. Then, it keeps the numerous powder products in separate silos. In this scenario, humidity regulates these tiny particles’ liquidity, thus depositing in the several receptacles that supply the future decorative surfaces. These travel between the channels that provide other decoration components or allow them to move during blending systems.
Decorating, Shaping, and Baking of the Versatile and Powerful Dekton
- Decoration of the slabs:These nanoparticles are carefully positioned in multiple places on a belt, forming a continuous slab, employing several unique processes for their design and function. The manufacturer creates various aesthetic impacts using these decorating systems. The company can create different effects throughout the slab’s thickness or only on its surface. In all, and during the initial production stage, 16 separate ornamental systems can function independently, together, or in groupings, resulting in an extraordinary creative variety of materials.
- Shaping Dekton:manufacturer divides the continuous slab into various portions that will ultimately be combined to form the final slab, which the brand exposes to an intense ultra-compaction procedure. To accomplish this, Cosentino uses a one-of-a-kind press with particular sizes and global compacting capabilities.
- Thermal process: the manufacturer gives the slab its ultimate physical, chemical, and aesthetic qualities during this stage. It uses up to 1300 Celsius temperatures, ensuring that the different coloured particles respond consistently. Then, the brand converts the raw material and pigments into other transitory composites. Finally, the process regulates these composites using heat to react and take the correct synthesis process.
Dekton worktops provide numerous advantages for both home and office environments. They meet all technical criteria to transform interior or outdoor designs into highly durable surfaces.
A Wide Range of Colours
With fifty different colours across seven collections, Dektonworktops offer endless combinations of colour, finish, and thickness. Whether you prefer traditional or contemporary designs, the seven collections—Natural, Tech, Solid, Industrial, Liquid, and Stonika—cover every design style and theme.
Scratch and Abrasion Resistant
Dekton countertops offer superior scratch and abrasion resistance, with a wear volume average abrasion of 116 mm3. This makes them almost 5.5 times more resistant than marble, with an abrasion wear of 22.23 mm3, making them ideal for high-use areas.
Unrivalled Thermal Shock Resistance
Unlike natural stones like marble and granite or engineered stones like quartz, Dekton worktops withstand extreme temperature changes. They can handle up to 300 degrees Celsius, letting you place hot items directly on the surface without fear of cracking, burning, or scorching.
Fireproof
Dekton is rated Class A1 according to the UK's BS EN 13501-1 regulation, the highest performance rating for fire resistance. This means it can tolerate direct contact with heated cookware and devices without getting burned, ensuring your kitchen remains safe and durable.
Easy to Clean
Unlike other materials, a Dekton kitchen worktop isn't affected by bleach or acids. Spray any household cleaner on the surface for quick clean-ups, making it perfect for kitchen and bathroom areas where messes are frequent.
Low Maintenance
One of Dekton's biggest advantages is its low maintenance. The surface doesn't require sealants, additional coatings, primers, or enhancers, which translates to significant time and cost savings over other worktop materials that demand regular upkeep.
Stain Resistant
Dekton can withstand common kitchen ingredients like wine, turmeric, coffee, lemons, and ketchup, ensuring your work surface remains pristine. Use a spray like Windolene or water and neutral soap for daily cleaning.
Dimensional Stability
Dekton's large slab sizes of 3200 x 1440 mm allow for efficient planning and installation, reducing material waste and cost. The slabs expand minimally, ensuring tight seams between worktops.
High Mechanical Strength
The pressing process, with up to 25,000 tonnes, gives Dekton its unmatched mechanical strength. Its compactness offers versatility in five thickness options, making it suitable for areas requiring high-impact resistance.
UV Light Resistance
Ideal for indoor and outdoor applications, Dekton worktops are highly resistant to UV light, ensuring they do not fade or deteriorate over time.
High Resistance to Hydrolysis
Dekton's superior resistance to hydrolysis makes it perfect for application in bathrooms, spas, and outdoor pools. The surface does not split or deteriorate, ensuring long-term durability.
Resistant to Freezing and Thawing
Designed to withstand diverse weather conditions, Dekton's resistance to freezing and thawing ensures it performs exceptionally well, even in extreme climates.
CHEMICAL FORMULATION
Because this stonecontains no resins or organic ingredients, Dekton does not employ a polymerisation process during its manufacture, and its chemical makeup is entirely inorganic.
In addition, DEKTONuses several formulas that vary according tothe surface type, meaningthat the final chemical structure can change without affecting itschemical or physical qualities.
Aluminium silicates, amorphous silica, crystalline silica, zircon, and inorganic colours are a few examples of DEKTON's chemical makeup. The crystalline silica component in all colours and formulations are alwaysless than 11% by weight.
TECHNICAL CHARACTERISTICS
TEST | STANDARD | DETERMINATION | Units | Family i | Family ii | Family iii |
---|---|---|---|---|---|---|
Flexural and bending strength | UNE EN ISO 10545-4 | Average flexural strength |
N |
60 | 67 | 59 |
UNE EN ISO 10545-4 | Average bending load | N | 2.548 | 2.313 | 2.356 | |
UNE EN ISO 10545-4 | Average bending strength | % | 14.966 | 13.559 | 13.818 | |
Water absorption, open porosity and densities | UNE EN ISO 10545-3 |
Boiled water absorption |
% |
0 |
0,1 |
0,1 |
UNE EN ISO 10545-3 | Vacuum water absorption | % | 0,1 | 0,1 | 0,1 | |
UNE EN ISO 10545-3 | Open porosity | % | 0,2 | 0,2 | 0,2 | |
UNE EN ISO 10545-3 | Apparent relative density | g/cm | 2,51 | 2,61 | 2,53 | |
UNE EN ISO 10545-3 | Apparent density | g/cm | 2,50 | 2,61 | 2,52 | |
Resistance to deep abrasion | UNE EN ISO 10545-6 | Abrasive volume | mm3 | 125 | 106 | 115 |
Determination of dimensions and surface aspect | UNE EN ISO 10545-5 C | Coefficient of average restitution | - | 0.85 | 0.85 | 0.85 |
Determination of thermal linear dilation | UNE EN ISO 10545-8 | Dilatation between 30-100ºC | ºC-1 | 6,5. 10-6 | 5,1. 10-6 | 0,3. 10-6 |
Determination of thermal shock resistance | UNE EN ISO 10545-9 | Damage | - | Approved / undamaged | Approved / undamaged | Approved / undamaged |
Determination of humidity dilation | UNE EN ISO 10545-10 | Maximum expansion | mm/m | 0.1 | 0.1 | 0.1 |
Average expansion | mm/m | 0.0 | 0.0 | 0.0 | ||
Determination of freeze resistance | UNE EN ISO 10545-12 | Damage | - | Approved / undamaged | Approved / undamaged | Approved / undamaged |
Determination of chemical resistance | UNE EN ISO 10545-13 | ClNH4 / Cleaning products | Class | UA (undamaged) | UA (undamaged) | UA (undamaged) |
Bleach / Salts for pools | Class | UA (undamaged) | UA (undamaged) | UA (undamaged) | ||
HCl (3% v/v) | Class | UA (undamaged) | UA (undamaged) | UA (undamaged) | ||
Citric Acid (100 g/l) | Class | UA (undamaged) | UA (undamaged) | UA (undamaged) | ||
KOH (30 g/l) | Class | UA (undamaged) | UA (undamaged) | UA (undamaged) | ||
HCl (18%) | Class | UA (undamaged | UA (undamaged | UA (undamaged | ||
Lactic Acid (5%) | Class | UA (undamaged | UA (undamaged | UA (undamaged | ||
KOH (100 g/l) | Class | UA (undamaged | UA (undamaged | UA (undamaged | ||
Determination of stain resistance | UNE EN ISO 10545-14 | Agente green | Class | 5 | 5 | 5 |
Agente red | Class | - | - | - | ||
Iodine (solution) | Class | 5 | 5 | 5 | ||
Olive Oil | Class | 5 | 5 | 5 |
TECHNICAL SPECIFICATIONS
TEST | STANDARD | DETERMINATION | UD | Family i | Family ii |
---|---|---|---|---|---|
Moisture expansion | ASTM C370 | Average moisture expansion | % | 0.02 | 0.005 |
Breaking strength | ASTM C648 | Average breaking strength | Ibf | 3963 | 4896 |
Flexural properties | ASTM C674 | Average modulus of rupture | psi | 10828 | 13997 |
Water absorption, bulk density, apparent porosity and apparent specific gravity | ASTM C373 | Average water absorption | % | 0.03 (Impervious) | 0.05 (Impervious) |
Static coefficient of friction (skid resistance) | ASTM C1028 | Static coef. Friction dry | - | 0.80 | 0.77 |
Static coef. Friction wet | - | 0.66 | 0.56 | ||
Wet dynamic coefficient of friction (DCOF) | ANSI A126.1 section 9.6.1 | Average DCOF | - | 0.57 | |
Relative resistance to wear (Taber abrasion) | ASTM C501 | Average Abrasive Wear Index | 182.2 | 337 | |
Thermal shock resistance | ASTM C484 | Defects | No Defects | No Defects | |
Bond strength | ASTM C482 | Average bond strength | psi | 423 | 437 |
Resistance to chemical substances | ASTM C650 | Common Household and cleaning chemicals | % | ||
Acetic acid, 3% (v/v) | - | Not affected | Not affected | ||
Acetic acid, 10% (v/v) | - | Not affected | Not affected | ||
Ammonium chloride, 100 g/L | - | Not affected | Not affected | ||
Citric acid solution, 30 g/L | - | Not affected | Not affected | ||
Citric acid solution, 100 g/L | - | Not affected | Not affected | ||
Lactic acid, 5% (v/v) | - | Not affected | Not affected | ||
Phosphoric acid, 3% (v/v) | - | Not affected | Not affected | ||
Phosphoric acid, 10% (v/v) | - | Not affected | Not affected | ||
Sulfamic Acid, 30 g/L | - | Not affected | Not affected | ||
Sulfamic Acid, 100 g/L | - | Not affected | Not affected | ||
Swimming pool chemicals | - | Not affected | Not affected | ||
Sodium hypochlorite solution, 20 mg/L | - | Not affected | Not affected | ||
Acids and bases | |||||
Hydrochloric acid solution, 3% (v/v) | - | Not affected | Not affected | ||
Hydrochloric acid solution, 18% (v/v) | - | Not affected | Not affected | ||
Potassium hydroxide, 30 g/L | - | Not affected | Not affected | ||
Potassium hydroxide, 100 g/L | - | Not affected | Not affected | ||
Absorption and bulk gravity | ASTM C97 | Average weight per cent absorption | % | 0,02 | 0,04 |
Average density | Ib/f | 156 | 160,63 | ||
Modulus of rupture | ASTM C99 | Average modulus of rupture dry conditions | psi | 8128 | 9042 |
Average modulus of rupture wet conditions | psi | 7490 | 8446 | ||
Flexural strength | ASTM C880 | Average flexural strength dry conditions | psi | 6840 | 3118 |
Average flexural strength wet conditions | psi | 6205 | 4187 | ||
Compressive strength | ASTM C170 | Average compressive strength dry conditions | psi | 34409 | >55000 |
Average compressive strength wet conditions | psi | 17823 | >55000 | ||
Abrasion resistance | ASTM C1353 | AverageAbrasion Index | - | 349 | 349,48 |
SLIP RESISTANCE REPORT
According to STANDARD EN -14.631Family I (Spectra, Domoos, Sirius, Sirocco, Kadum, Strato, Keranium, Ananké)
Finish | NATURAL | NATURAL | SLATE | SLATE | WOOD | WOOD | POLISHED | POLISHED |
Colour | PDomoos / Strato / Sirocco / Kadum / Keranium | PDomoos / Strato / Sirocco / Kadum / Keranium | Sirius | Sirius | Ananké | Ananké | Spectra | Spectra |
Determination | PSRV dry | PSRV wet | PSRV dry | PSRV wet | PSRV dry | PSRV wet | PSRV dry | PSRV wet |
Value | 48 | 23 | 49 | 22 | 44 | 21 | Pending Test | Pending Test |
COLOUR AND TONES
Cosentino assigns numbers to describe tones in the colours (slight changes in coloUr intensity), and each slab is defined by Colour &Tone.
Here are the factors that determine Dekton colours and tonevariation:
- Colours in solids: E variant (control with) The slab unit label with Colour and Tone Code reflects the colour and tone.
- The label determines the slab's Tracing and its history. As it progressesthrough the industrial manufacturing operation via the slab number (batch).
- Spectrophotometer settings: Lab/D65/10o).
- Colours with veins: visible differences (of pattern)
Dekton: 25-year warranty
Besides technical superiority, originality, and style, Dekton offers a 25-year warranty on its designs.
You need to provideyour invoice/receipt when filling out the Dekton warranty form within 6 (six) months of your purchase to activate your warranty.
If you don't activate your warranty within this period, you will enjoy the same benefits for 2 (two)years.
RETURNS AND SHIPPING POLICY RETURNS
Except for damaged surfaces, all sales are final. Please call 020 39760029 or email HELLO@WORKTOPLIBRARY.CO.UK for more information before mailing exchanges or online purchasing return products installed in faulty or damaged condition.
SHIPPING \ TURNAROUND
We process all orders within one business day. However, specific stones may have longer lead times due to high demand or special-order items from other countries.
DELIVERY & INSTALLATION COSTS
We compute delivery and installation costs at the time of purchase. Our team of professional stone fitters install all stone surfaces.
Installation and delivery charges vary depending on weight, site access, and delivery location from our workshop in West London, United Kingdom.
INSTALLATION & DELIVERY ADDRESSES
Stone worktop installation is available in London and 150 miles surrounding areas. Don't hesitate to get in touch with our Worktop Library Service Team at (20) 39760029.
Reviews
There are no reviews yet.